Boom Supersonic Partners with Stratasys to Bring 3D Printed Parts to the XB-1 Supersonic Demonstrator
Boom Supersonic is a company with an out-sized and incredibly ambitious dream: to make supersonic air travel a reality. Boom wants to make a passenger aircraft capable of going at Mach 2.2 with a range of 8300 kilometers. Imagine if we could travel in an aircraft that went 2300 kilometers an hour, the world would be a lot closer then. Rome to Beijing in four hours instead of eight or New York to Paris in around three and a half hours. The technical challenges abound for such an achievement. Last time with Concorde supersonic air travel remained a niche hampered by very high seat mile costs and limited availability due to noise pollution from supersonic booms. Boom maintains that it can make the economics of supersonic air travel work this time around. It is aiming for transatlantic ticket prices of around $5000 which would make it accessible for a larger group of executives and wealthy people than the passenger car level prices of the Concorde.
But, the Concorde was a prestige project that had two countries working together to make it happen. Can one firm now leverage composites and modern technology to leapfrog Boeing and Airbus in creating a completely renewed air travel category? Boom is betting that it can and one of the things it is turning to is FDM. The company will use a Stratasys F900 Fortus system to make in-flight parts for its aircraft. The firm already uses the Fortus to make parts for the XB-1, the baby boom which is a one third scale demonstrator aircraft which is due to be flight tested this year and has a partnership in place with Stratasys.
Stratasys has announced that Boom has got the Aircraft Interiors Solution package, a set of add ons for people making aircraft interiors, similar to the Manufacturing package that they also have. The AIS is meant to help aviation companies qualify and produce aviation compliant parts. Aircraft interiors are somewhat of an unsung hero of 3D printing. Whereas it is well known that Airbus, GE an Boeing are betting on a lot more 3D printed parts in aircraft it is in the interior of cabins that 3D printing has made the most progress so far. Polymer parts, often out of PEI (Ultem) make AEC ducting, parts in kitchenettes, parts such as Audiovisual housings, parts in toilets and more. Even commercial aviation is rather low volume when you compare it to things like cars. In general aviation, private jets often have a lot of custom components in them and these are often 3D printed. Especially B side components and stuff behind walls is where 3D printing shines in the dark.
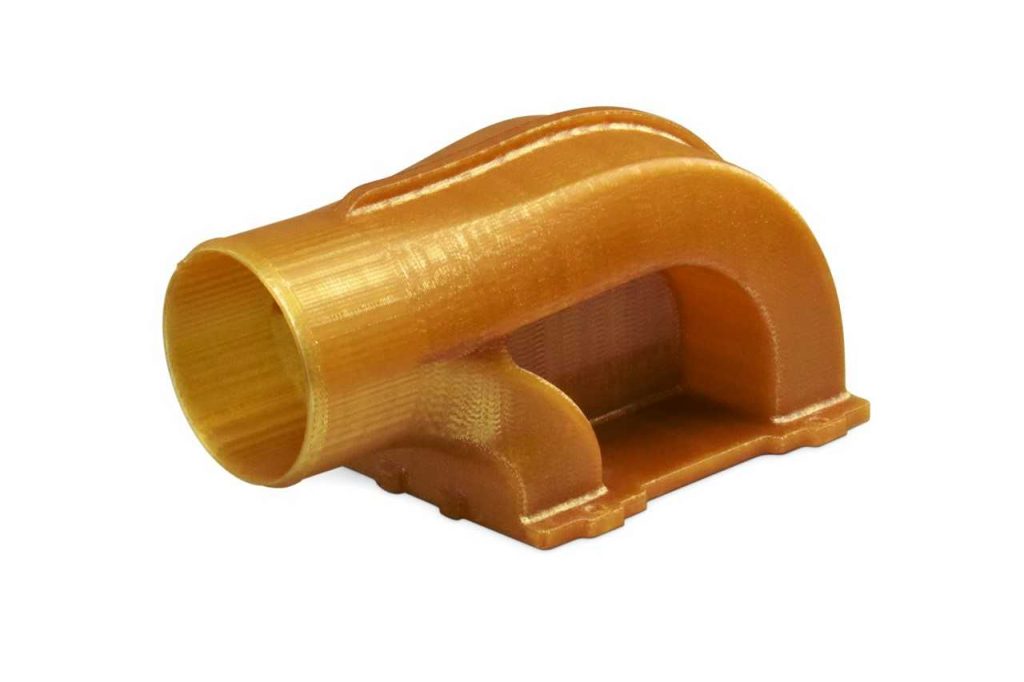
What do you think? PEI? Looks a lot like Ultem 1010 to me?
Mike Jagemann, Head of XB-1 Production at Boom, said,
“By being able to print critical parts and components on site rather than purchasing them from a supplier, we can create custom parts, increase our speed from engineering to manufacturing, and focus on building the aircraft and fulfilling our vision. During the first three years of our partnership, we 3D printed more than 200 parts for tooling, prototypes and test benches using Stratasys’ F370 and Fortus 450mc 3D printers, and have saved hundreds of hours of work time, enabling rapid iteration of design cycles.”
Post XB-1, Stratasys hopes that 3D printed parts will make it onto the full sized supersonic airliner Overture.
Rich Garrity, President Americas, Stratasys, said,
“The team at Boom is doing something that’s never been achieved – successful mainstream supersonic airline travel. But development of aircraft that can safely and efficiently travel at Mach 2.2 requires a new approach to manufacturing processes. Working together, our teams have put the technology to work for efficient, reliable and repeatable prototypes, tooling and jigs and fixtures. Now, we’re ready to go further – for strong, durable, lightweight production-grade aircraft parts.”
Again this quote deftly points out what we are seeing in many industries jigs and fixtures are the gateway drug to 3D printing in manufacturing. Lightly regulated when compared to qualified aviation parts jigs and fixtures are the way for manufacturing teams to gain familiarity with 3D printing. A part that is made to aid them and reduce errors is sure to be popular on the concrete floor. And if that part can be made without riding roughshod over everyone’s carefully documented processes then it may actually be adopted. In consumer electronics, automotive and aviation we’re seeing that 3D printing jigs and fixtures is the best path to getting companies to adopt 3D printing more widely in production. You can either give him an excuse to say no to changing his entire process or reach out to give her a tool that will make her life easier. In that sense jigs and fixtures are perfect to in a non-critical but hands-on way introduce companies to 3D printing.
I hope that at one point we get to find out what materials the Boom team will be using. Will they opt for tried and true Sabic Ultem? Or will they be roadmapped into Solvay PEEK or perhaps could they go for Arkema’s PEKK? Or will the team want filled grades of either one of these materials for higher stiffness or strength? Somewhere away from view, the war for the future high-performance polymers in aviation is being fought and won by people with clipboards.
Subscribe to Our Email Newsletter
Stay up-to-date on all the latest news from the 3D printing industry and receive information and offers from third party vendors.
Print Services
Upload your 3D Models and get them printed quickly and efficiently.
You May Also Like
3D Printing News Briefs, August 16, 2025: European Distribution, Expeditionary Powder, & More
We’re taking care of business first today in 3D Printing News Briefs, with Wayland Additive appointing a new Chief Technology Officer and AML3D expanding its European distribution. Moving on, Metal...
A Growing Area of Interest: 3D Printed Kirigami Sensors
Kirigami is a Japanese art and craft form where paper is cut and folded into intricate shapes. Often these shapes, accordion-like, can unfold into striking new forms. Whereas origami stretches...
Farsoon and Stark Future Push Titanium 3D Printing for Electric Motorbikes
Farsoon and Stark Future have taken a big step in their partnership. The two companies are already doing serial production of functional parts for Stark’s electric motorbikes. However, their new...
EOS & NASA Sign Agreement to Accelerate Space 3D Printing Workforce Development
If there’s one major issue in the manufacturing sector that can be expected to persist well into the future, it’s workforce development. This is especially true in nations like the...